How to Test Capacitors for Reliability and Performance in 2024: The Ultimate Guide
Blog
2024-11-21
Richmon
Testing capacitors isn’t just about finding failures – it’s about preventing them. In today’s electronic devices, where components are pushed to their limits, proper capacitor testing can mean the difference between a reliable system and costly downtime. At Richmon, we’ve seen firsthand how regular testing prevents up to 80% of potential capacitor-related failures.
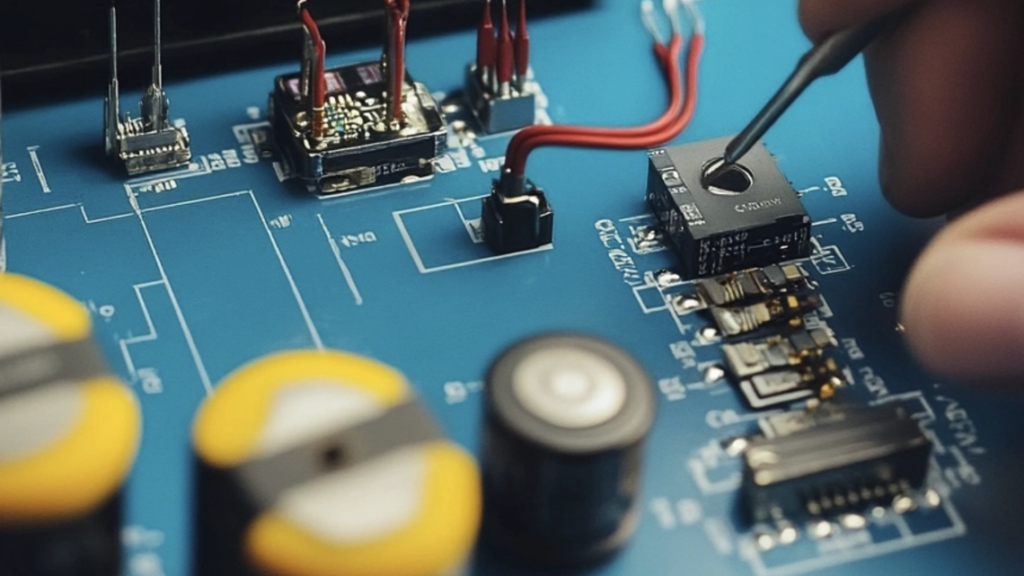
Table of Contents
Types of Capacitors and Their Testing Requirements
Different capacitors need different testing approaches. Here’s what you need to know about each type:
Electrolytic Capacitors
- Main Use: Power supplies and filtering
- Critical Tests: ESR, leakage current, capacitance value
- Warning Signs: Bulging tops, leaking electrolyte
Ceramic Capacitors
- Main Use: High-frequency applications
- Critical Tests: Capacitance value, temperature stability
- Warning Signs: Cracks, chipping, discoloration
Tantalum Capacitors
- Main Use: Mobile devices and medical equipment
- Critical Tests: Leakage current, ESR
- Warning Signs: Burning smell, physical damage
Key Parameters You Must Test
Focus on these essential measurements for reliable results:
Capacitance Value: Should be within ±10% of rated value
ESR (Equivalent Series Resistance): Lower is better, compare against datasheet
Leakage Current: Should be below maximum specified value
Voltage Rating: Must match application requirements
Testing Tools: What You Need in 2024
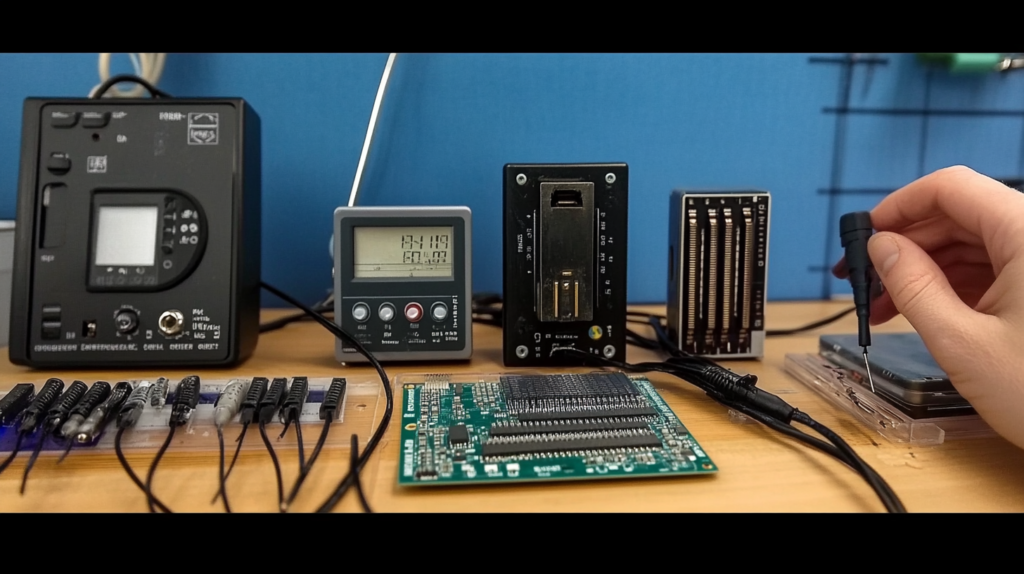
Modern capacitor testing requires specific tools. Here’s your essential toolkit:
Basic Tools
- Digital Multimeter: For basic capacitance and voltage tests
- ESR Meter: For measuring equivalent series resistance
- LCR Meter: For precise impedance measurements
Advanced Equipment
- Automated Testing Systems: For high-volume testing
- Temperature Chambers: For environmental testing
- Data Loggers: For long-term monitoring
Need professional testing equipment? Check out our complete testing solutions.
Step-by-Step Testing Procedure
- Safety First:
- Discharge the capacitor completely
- Wear safety glasses and gloves
- Use insulated tools
- Initial Check:
- Visual inspection for damage
- Check voltage rating
- Verify polarity for electrolytics
- Testing Steps:
- Measure capacitance
- Check ESR readings
- Test for leakage
Interpreting Your Test Results
Reading Type | Good Range | Action Needed |
---|---|---|
Capacitance | ±10% of rated value | Replace if outside range |
ESR | Under manufacturer spec | Replace if higher |
Common Failure Modes and Predictive Maintenance
Understanding failure modes helps prevent system breakdowns. Here are the most common issues:
- Physical Damage: Cracks, bulges, or leaks
- Electrical Issues: High ESR, low capacitance
- Temperature Problems: Overheating, thermal runaway
- Age-Related: Dried electrolyte, wear-out failures
2024 Technology Trends in Capacitor Testing
The field of capacitor testing is evolving rapidly. Here are the latest innovations:
- AI-Powered Testing: Automated fault detection and prediction
- IoT Integration: Remote monitoring and real-time data analysis
- Advanced Analytics: Predictive maintenance capabilities
Useful External Resources
Take Your Capacitor Testing to the Next Level
Proper capacitor testing is crucial for maintaining reliable electronic systems. With the right tools and knowledge, you can significantly reduce failure rates and extend component life.
Ready to Improve Your Testing Process?
Looking to source reliable capacitor for your business?
Contact us today for expert assistance and access to a wide range of capacitor solutions.
Recent Posts
- Avoid 5 Critical Mistakes When Sourcing Chip for Industrial Applications
- Avoid 5 Critical Mistakes When Sourcing ADCs for Industrial Applications
- Avoid 5 Critical Mistakes When Sourcing Memory Chips for Industrial Applications
- Avoid 5 Critical Mistakes When Sourcing MCUs for Industrial Applications
- Avoid 5 Critical Mistakes When Sourcing PMICs for Industrial Applications